خدمات پایش وضعیت
مدیر سایت
فروردین ۲۱, ۱۴۰۱
1۰173
درباره ما
پایش وضعیت قسمت اصلی نگهداری و تعمیرات در صنایع است. رویکرد یکپارچه به موضوع نگهداری و تعمیرات بر اساس وضعیت یا نگهداری و تعمیرات پیش گویانه داری منافع و مزایای بسیاری است. از جمله جلوگیری از بروز خطای ناخواسته در سیستم، کاهش زمان و هزینه تعمیرات و … که باعث شده در صنایع مهم از جمله نیروگاهها مورد توجه قرار گیرد. ار تکنیکهای پایش وضعیت در تجهیزات الکتریکی می توان به آنالیز ارتعاشات، آنالیز جریان، آنالیز دما و آنالیز روغن اشاره کرد. مزیت بزرگ ترموگرافی نسبت به ابزارهای سنتی اندازه گیری دما، نمایش طیف حرارتی است. با استفاده از این طیف می توان توزیع دما روی سطح را بصورت یکپارچه مشاهده نمود و خیلی سریع محل عیب را تشخیص داد. از دیگر مزایا عدم نیاز به بی برق کردن تجهیزات مهم جهت تشخیص خطا است. مزیت دیگر جلوگیری از کاهش عمر تجهیزات است، از آنجا که طبق فرمول آرهنیوس رابطه دما و کاهش عمر بصورت نمایی است. پایش پیوسته دمایی تجهیزات و اقدام در جهت رفع عیوب جزئی و کاهش دمای تجهیزات، می تواند باعث افزایش عمر گردد.
شرکت مدیریت تولید برق طوس سابقه ۳۵ ساله در زمینه تعمیرات و نگهداری نیروگاهی دارد که در کنار تعمیرات EM تعمیرات CM نیز در دستور کار می باشد. یکی از روشهای پایش وضعیت تجهیزات الکتریکی ترموگرافی است که بصورت کاملا حرفه ای با دوربین پیشرفته انجام می شود.
خدمات ترموگرافی توسط دوربین پیشرفته و تحلیل کارشناسان مجرب برای کلیه تجهیزات در تمامی شرکتهای استان خراسان قابل انجام است.
جهت اطلاعات بیشتر با
شماره مستقیم
۰۵۱۳۵۴۲۱۹۲۰
یا ایمیل
info@tpgm.ir
تماس حاصل فرمایید.
انجام خدمات پایش وضعیت بوسیله آنالیز ارتعاشات
مقدمه
در مبحث نگهداری و تعمیرات به مجموعه اعمالی که با بررسی وضعیت ماشین و تغییرات آن در طول زمان بر اساس پارامترهایی مانند ارتعاشات، صدا، عملکرد، روانکاری، دما و … وضعیت ماشین را تعیین میکنند پایش وضعیت گفته میشود. پایش وضعیت یکی از اجزای اصلی نگهداری و تعمیرات پیشگیرانه میباشد.
نگهداری و تعمیرات پیشگیرانه در چند دهه اخیر بیشترین کاربرد را در روشهای تعمیراتی در کشورهای پیشرفته داشته است. در این روش وضعیت ماشین آلات را بررسی و آنها را در فواصل زمانی مشخصی بازدید میکنند که البته این فواصل زمانی به اهمیت تجهیز بستگی دارد. در صورت مشاهده هر نوع خرابی سرعت رشد آن را تحت نظر قرار میدهند؛ و در زمانی قبل از تخریب دستگاه آن را از سرویس خارج و به تعمیر همان قسمت معیوب که از قبل تعیین شده بود میپردازند.
با توجه به اینکه قبل از توقف ناخواسته دستگاه را از سرویس خارج میکنیم در نتیجه خسارات و هزینههای ناشی از توقف ناخواسته دستگاه از بین رفته و از خراب شدن سایر قسمتهای تجهیز نیز جلوگیری میشود.
مهمترین روشهایی که در صنایع بزرگ خصوصا نیروگاه ها جهت پایش وضعیت تجهیزات به کار گرفته میشود عبارتند از:
- آنالیز ارتعاشات
- آنالیز روغن
- ترموگرافی
- آنالیز صدا
- آنالیز جریان
به جرات میتوان گفت مهمترین و کاربردی ترین روش پایش وضعیت در صنایع آنالیز ارتعاشات میباشد.
آنالیز ارتعاشات، ابزار اصلی شناسایی عیوب و مراقبت از ماشین آلات دوار در دنیا میباشد.
نیروهای ارتعاشزا از نوع نیروهای دینامیکی هستند که بر اثر وجود کاستیهایی در ماشین ایجاد می شوند. برخی از زمینههای بروز کاستی (اختلاف از حالت ایدهآل) عبارتند از:
- محدودیتهای طراحی و ساخت
- اشکالات در نصب اولیه
- اشکالات بهره برداری
- اشکالات حین تعمیرات
از آنجاییکه رسیدن به حالت ایدهآل امکانپذیر نیست، همیشه تا حدی لرزش و ارتعاش در ماشین آلات وجود دارد که مجاز شمرده میشود. اما با گذشت زمان و بر اثر بروز اشکالات بعدی، بعضاً ارتعاشات نسبت به حد مجاز افزایش مییابد که با آنالیز و انجام اقدام اصلاحی مناسب، میتوان وضعیت را به حالت قبل برگرداند.
برخی از عوامل ایجاد نیروهای ارتعاش زا در ماشین آلات، عبارتند از:
- میس الایمنتی (عدم هم محوری)
- نامیزانی جرمی (آنبالانسی)
- سایش اجزا و قطعات
- نیروهای آیرودینامیکی و هیدرودینامیکی
- نیروهای الکترومغناطیسی
- تماس قطعات متحرک و ثابت
- اصطکاک
برخی عیوب قابل شناسایی از طریق آنالیز ارتعاشات عبارتند از:
- نامیزانی جرمی
- تشدید (رزونانس)
- لقی مکانیکی
- خمیدگی محور
- خرابی بیرینگ
- خرابی چرخدنده
- فونداسیون معیوب
- اشکالات الکتریکی
- اشکالات آئرودینامیکی و هیدرودینامیکی
- خرابی کوپلینگ
- خرابی تسمه و پولی
- خارج از مرکزی
آنالیز ارتعاشات به عنوان یکی از روشهای پایش وضعیت دارای دو مرحله اساسی میباشد.
مرحله اول: اندازه گیری ارتعاشات و مقایسه مقادیر ارتعاشات با استانداردهای موجود و نیز مقادیر گذشته
مرحله دوم: در صورتیکه مقادیر اندازه گیری شده از حد توصیه شده استاندارد بالاتر بوده و یا نسبت به گذشته افزایش قابل توجهی داشته باشد بایستی آنالیز ارتعاشات صورت گیرد. روشهای مرسوم برای آنالیز ارتعاشات عبارتند از:
- آنالیز فرکانسی
- آنالیز شکل موج زمانی (Time signal)
- آنالیز زاویه فاز
- آنالیز اوربیت
- آنالیز مشخصه های بیرینگهای غلتشی (BC)
- و ….
شرکت مدیریت تولید برق طوس سابقه ۳۵ ساله در زمینه تعمیرات و نگهداری نیروگاهی دارد که در کنار تعمیرات EM تعمیرات CM نیز در دستور کار می باشد. یکی از روشهای پایش وضعیت تجهیزات دوار آنالیز ارتعاشات است که بصورت کاملا حرفه ای با دستگاه ایزی وایبر انجام می شود.
تکنیک آنالیز ارتعاشات در نیروگاه طوس در فواصل زمانی مشخص جهت پایش وضعیت ماشین آلات دوار از جمله مجموعه توربوژنراتور، پمپهای آب تغذیه، پمپهای آب کندانس، پمپهای آب خنک کن، پمپهای سوخت مایع، فن های هوای احتراق، فن های سیرکوله دود، فن های هوای بویلرهای کمکی، فن های هوای خنک کن، فن های کندانسور، کمپرسورهای هوای کنترل و سرویس و …. به کار گرفته میشود.
بر این اساس برای هر تجهیز یک پرونده ارتعاشی تشکیل و سوابق ارتعاشات آن و وضعیت ارتعاشات در مقایسه با استاندارد برای آن ثبت میگردد (Rout). در صورت وجود ارتعاشات غیرمجاز آنالیز ارتعاشات با روشهای گفته شده در بالا انجام و عیب یابی صورت میگیرد. نهایتا پیشنهادات جهت رفع عیب به امور تعمیراتی ارائه و در زمان مقتضی اصلاحات لازم صورت میگیرد. پس از آن مجددا ارتعاشات اندازه گیری شده و نتیجه اصلاحات صورت گرفته مشخص میشود.
همچنین برای سایر تجهیزات نیز بنابر تشخیص امورهای بهره برداری و تعمیرات اندازه گیری و تحلیل موردی ارتعاشات انجام میگردد.
دستگاه ایزی وایبر با توجه به داشتن سنسور تاکومتر و دو سنسور ارتعاشی شتاب سنج قابلیت انجام پروسه بالانس را نیز دارا میباشد که بر اساس شرایط تجهیزات این فعالیت نیز در فعالیتهای پایش وضعیت نیروگاه انجام میشود.
خدمات آنالیز ارتعاشات توسط دوربین دستگاه ایزی وایبر و تحلیل کارشناسان مجرب برای کلیه تجهیزات در تمامی شرکتهای استان خراسان قابل انجام است. جهت اطلاعات بیشتر و با شماره مستقیم ۰۵۱۳۵۴۲۱۹۲۰ یا ایمیل info@tpgm.ir تماس حاصل فرمایید.
در ادامه نمونه ای از تجربیات آنالیز ارتعاشات در نیروگاه طوس ارائه شده است. گزارش زیر مربوط به پایش وضعیت ارتعاشات اف دی فن دو واحد سه نیروگاه میباشد.
همانطور که ملاحظه میشود روند افزایشی ارتعاشات و قرار گرفتن مقادیر در محدوده غیرمجاز توسط پایش وضعیت ارتعاشات با دستگاه ارتعاش سنج ثبت شده است.
پس از بررسی و تحلیل های صورت گرفته بر روی نمودارهای آنالیز فرکانسی و زاویه فاز، عیب موجود آنبالانسی در کوپلینگ هیدرولیکی اف دی فن تشخیص داده شد. یکی از عوامل ایجاد آنبالانسی در کوپلینگها نیز رسوب روغن در اطراف دیواره های کوپلینگ به دلیل دمای بالا می¬باشد که در اثر شوک ایجاد شده در کوپلینگ قسمتی از رسوبات روغن از جای خود کنده شده و باعث بر هم خوردن تعادل کوپلینگ می گردد. لذا اف دی فن متوقف و به دلیل کمبود وقت یک کوپلینگ از قبل آماده شده جایگزین آن شد که پس از راه اندازی مجدد کاهش چشمگیر ارتعاشات مشاهده شد. مقادیر ارتعاشات قبل و بعد از تعویض کوپلینگ در زیر مشاهده می شود.
در تصاویر زیر رسوبات زیاد روغن پس از دمونتاژ کوپلینگ معیوب که عامل اصلی ایجاد ارتعاشات بوده است قابل مشاهده می باشد.
در زیر نمودارهای ترند مربوط به جهت افقی یاتاقانهای ۱ و ۲ نمایش داده شده است. در این نمودارها به خوبی روند تغییرات ارتعاشات در مقاطع مختلف و نیز تاثیر تعویض کوپلینگ در کاهش چشمگیر میزان ارتعاشات دیده می شود.
در صورتیکه عیب سیستم به موقع تشخیص داده نمی شد امکان افزایش بیشتر ارتعاشات و در نتیجه آسیب رسیدن به یاتاقانها و نیز کوپلینگ هیدرولیکی محتمل بود.
همچنین با توجه به تشخیص درست مشکل، کل زمانی که صرف تعویض کوپلینگ، شارژ روغن و الایمنت این اف دی فن گردید کمتر از پنج ساعت بود. در این پنج ساعت واحد با بار نیمه (حدود ۷۵ مگاوات) در مدار بود لذا محدودیت تولید در این پروسه حدود ۳۷۵ مگاوات ساعت بود. در حالیکه اگر تشخیص صحیح عیب توسط پایش وضعیت صورت نگرفته بود مسلما زمان خیلی بیشتری جهت عیب یابی و رفع عیب سیستم مورد نیاز بود که متعاقبا محدودیت تولید بیشتری را به نیروگاه تحمیل می کرد.
طی چند سال اخیر که پایش وضعیت به طور جدی تر در نیروگاه دنبال می گردد چندین مورد مشابه نمونه بالا رخ داده است که با تشخیص به موقع و صحیح عیب، از وقوع خرابی، محدودیت تولید و خسارت بیشتر جلوگیری شده است.
تکنیک آنالیز ترموگرافی به طور کلی در پایش وضعیت الکتروموتورها، ترانس های قدرت و توزیع، سوئیچگیرها، بریکرها، تابلوها و پانلهای الکتریک و ابزار دقیق، باتریها، شارژرها، اینورترها و . . . به منظور دست یابی به ، وضعیت بیرینگها و سیستم خنک کاری الکتروموتورها، ارزیابی وضعیت اتصال ناقص در ترمینالها و اتصالات، جریان نامتعادل، جریان زیاد، نقطه داغ ناخواسته در سوئیچگیرها و ترانسفورماتورها و تابلوها و تشخیص سلولهای سوخته در باتری خانه ها
در ادامه برخی تجربیات در این زمینه آورده شده است.
موتورهای الکتریکی
الکتروموتورها یکی از تجهیزات پرکاربرد واحدهای صنعتی از جمله سیکل بخار می باشد. عیب یابی و رفع عیب به موقع آنها نقش اساسی در پایایی واحدها خواهد داشت. در بحث پایش وضعیت الکتروموتورها، روشهای مختلفی وجود دارد از جمله اندازه گیری لرزش، ترموگرافی، اندازه گیری صوت و آنالیز جریان که هر کدام تعدادی از عیوب را مشخص می کند. از آنجا که الکتروموتور یک وسیله الکتریکی-مکانیکی است بسیاری از عیوب مکانیکی توسط اندازه گیری لرزش قابل تشخیص است. همچنین برخی عیوب الکتریکی توسط آنالیز جریان (CSA) قابل تشخیص می باشد. علاوه بر این روشها، ترموگرافی نیز بعنوان روشی دیگر برای تشخیص عیوبی که ایجاد حرارت در سطح موتور می کند کاربرد دارد. به کمک ترموگرافی می تواند نا هم راستایی، مشکل در بلبرینگ، عدم خنک کنندگی و … در موتور تشخیص داده شود. هیچ کدام از روشهای عیب یابی، روش کاملی برای تشخیص تمام عیوب الکتروموتور نیستند و به تنهایی کارساز نمی باشد. همچنین تصمیم گیری فقط با اتکا به یک روش صحیح نیست و بهتر است از چند روش در کنار همدیگر استفاده شود.
بر اساس تجربه طیف نرمال برای الکتروموتورهای ۴۰۰ ولت مانند شکل ۱ است که نقطه داغ وسط الکترموتور قرار دارد و پروفایل خط فرضی A که در طول الکتروموتور کشیده شده است بعنوان مرجع در نظر گرفته می شود.
شکل ۱: یک نمونه طیف دمای الکتروموتور سالم و پروفایل دمایی خط فرضی
مشاهده میشود در این پروفایل انتهای موتور دمای کمتری دارد و به مرور دما افزایش پیدا می کند و به حداکثر می رسد سپس با حرکت به سمت کوپلینگ دما کاهش پیدا می کند. تلفات الکتریکی الکتروموتور که شامل تلفات فوکو هیسترزیس هسته و تلفات مسی سیم پیچ می باشد بصورت طبیعی باعث گرم شدن وسط الکتروموتور می گردد در صورت عیب مکانیکی یا خرابی بلبریگ طیف نرمال معرفی شده تغییر کرده و گرمای موضعی در محل خطا ایجاد می شود، مقدار دمای نقطه داغ و محل آن نشان دهنده نوع عیب می باشد. همچنین اگر فن الکتروموتور دچار مشکل شود نقطه داغ به سمت انتهای الکتروموتور متمایل خواهد شد و متوسط دمای کل سطح موتور افزایش پیدا خواهد کرد.
باید توجه شود که طیف دمایی به تنهایی کارساز نیست و مقدار حداکثر دما نیز ملاک عمل می باشد. به این صورت که ممکن است طیف دمایی طبیعی نباشد اماحداکثر دما زیر مقدار مجاز باشد، بدیهی است در این شرایط نیاز به اقدام فوری نمیباشد. در استانداردها مقدار حداکثر دمای موتور با توجه به کلاس عایقی مشخص شده است. در جدول ۱ مقادیر دمای مجاز طبق استاندارد IEC برای کلاسهای عایقی مختلف بیان شده است. همچنین استاندارد NEMA[۱] جدول شماره ۲ را معرفی کرده است. در این جدول مقادیر بصورت مقایسه ای بیان شده است.
این نکته ضروری است که دمای سطح اندازه گیری شده روی سطح است و با تبدیلهایی دمای داخل هسته و سیم پیچها قابل محاسبه است.
جدول۱: مقادیر مجاز دمای الکترموتور IEC
(حداکثر دما/افزایش دما/دمای محیط)
جدول۲: استاندارد NEMA برای مقایسه دما در تجهیزات الکتریکی
شکل ۲ یک نمونه الکتروموتور که دارای نقطه گرم در بلبرینگ طرف کوپلینگ است نمایش داده شده است. پروفایل خط A نسبت به الگوی معرفی شده انحراف دارد همچنین حداکثر دما نیز نزدیک مقادیر مجاز استاندارد است. لذا الکتوموتور زیر از محل بلبرینگ الکتروموتور سمت فن معیوب می باشد و نیاز به بازدید و سرویس دارد.
شکل ۳ یک نمونه دیگر الکتروموتور که دارای دمای بالا و طیف دمایی غیر طبیعی می باشد نمایش داده شده است. حداکثر دمای ۸۰ درجه سانیت گراد ثبت شده است که با در نظر گرفتن ۲۰ درجه بیشتر نزدیک محدوده غیر مجاز می باشد. در این نمونه روغن از گیربکس به داخل الکتروموتور نفوذ کرده و باعث گرمای الکتروموتور شده است. این عیب توسط اندازه گیری لرزش مشخص نشده است و جزو عیوبی است که فقط با ترموگرافی مشخص می گردد.
از دیگر کاربردهای ترموگرافی، تست وضعیت هسته الکتروموتورهاست (تست ELCID). در صورت صدمه به هسته شار بصورت موضعی تغییر کرده و تلفات هسته زیاد خواهد شد و در نقطه خطا دمای موضعی ایجاد می شود. در شکل زیر یک نمونه هسته معیوب مشاهده می شود. انجام این تست روی الکتروموتورهای تعمیری ضروری است.
ترانسفورماتورها
ترموگرافی عیوبی از ترانسها را که ایجاد حرارت در سطح ترانس می کند نشان میدهد. از جمله این عیوب مشکل در سیستم خنک کن، مشکل در اتصالات الکتریکی و نقطه داغ ناخواسته می باشد. از جدول ۲ در مورد ترانسها نیز می توان استفاده کرد به این صورت که نقاط همسان در ترانسهای مشابه (مثلا ترانسهای خروجی واحد) در شرایط بار یکسان ترموگرافی می گردد و بر اساس مقایسه و با معیار جدول ۲ اقدام لازم صورت می گیرد. ترانسها و اتصالات فشار قوی نیز مانند سایر تجهیزات مهم در برنامه ترموگرافی قرار دارد. در ادامه در شکل ۵ یک نمونه ترانس فشار قوی که دارای طیف حرارتی نرمال است مشاهده می گردد.
در این شکل قسمت پایین کولر سمت چپ دمای کمتری نسبت به قسمت بالای کولر دارد و نشان می دهد خنک کنندگی روغن به درستی در حال انجام است. در کولر سمت راست قسمتی از رادیاتورها دمای کمتری دارد و نشان دهنده عیب در پره ها می باشد که در اولین توقف باید مورد بازبینی و رفع عیب قرار گیرد.
در شکل ۶ طیف حرارتی ترانس قدرت دیگری نمایش داده شده است که در اتصالات خروجی یکی از بوشینگها دارای نقطه داغ غیر طبیعی می باشد. از آنجا که این نقطه داغ اختلاف دمای زیادی نسبت به قسمتهای مشابه در فازهای دیگر دارد همچنین دمای بالاتر از ۱۰۰ درجه سانتی گراد نشان دهنده عیب در آن نقطه می باشد و نیاز به پیگیری در اولین فرصت دارد.
اتصالات بریکرها
از موارد دیگر که در برنامه ترموگرافی قرار دارد بریکر ها است. استاندارد جدول زیر را برای حداکثر دما در بریکرها معرفی کرده است.
در شکل ۴ ترموگرافی یک نمونه بریکر معیوب که دارای دمای ۹۲ درجه سانتیگراد در نقطه داغ است آورده شده است. در ادامه بریکرهای دیگر نیز ترموگرافی گردید و مشاهده گردید حداکثر دمای بریکر مذکور نسبت به سایر بریکرهای مشابه بالاتر می باشد. لذا بریکر مذکور جهت بازدید و سرویس از مدار خارج گردید.
اتصالات و اِلمانهای تابلوها و کابینها:
از دیگر کاربردهای ترموگرافی عیب یابی تابلوها و کابینهای فشار ضعیف و متوسط میباشد. از آنجا که در زمانی که تابلو برقدار است امکان نزدیک شدن وجود ندارد، یکی از روشهای مناسب برای تشخیص محل دقیق خطا و کاهش زمان تعمیرات، ترموگرافی می باشد. بهترین روش برای تعیین شرایط نامطلوب مقایسه با یک حالت پایه است به این صورت که یک طیف مناسب بعنوان شرایط عادی وجود داشته باشد که عکسهای گرفته شده با آن شرایط پایدار مقایسه گردد. این حالت پایه می تواند مربوط به همان تابلو در زمان عادی باشد یا تابلوهای مشابه با شرایط بار مشابه باشد. در شکل ۵ یک تجربه عملی از تابلویی می باشد که ۵ کابین مشابه مقایسه شده اند. علاوه بر مقایسه، مقدار دمای نقطه داغ نیز معیار می باشد. جدول زیر بعنوان مقدار دما و اقدام مرتبط با هر بازه دمایی پیشنهاد شده است. در شکل ۵ دمای نقطه داغ کابین شماره ۲ از موارد مشابه حدود ۲۰ درجه بیشتر است همچنین دمای نقطه داغ داخل کابین حدود ۱۰۰ درجه بود.
در تصویر زیر یک نمونه اتصال ناقص در خروجی تابلوها آورده شده که باعث گرمای موضعی شده است.
باطریها
از دیگر تجهیزات مهم مجموعه باتری ها است. از آنجا که باتری ها مدام در مدار است و به ندرت از مدار خارج می گردد پایش آنلاین آنها نیز ضروری می باشد. از دیگر قابلیتهای ترموگرافی تشخیص عیوب مجموعه باتری خانه است. عیوب قابل تشخیص شامل عیب در اتصالات و عیب در سلولها است. استاندارد IEEE دمای ۱-۲ درجه سانتی گراد بالاتر از دمای محیط را بعنوان شرایط غیر طبیعی تلقی کرده است. شکل ۸ یک نمونه ترموگرافی سلول معیوب را نشان می دهد. همانطور که در شکل نیز مشخص است اختلاف دمای سلول معیوب بیشتر از ۱۰ درجه سانتی گراد است.
کانال کابلها
از دیگر موارد که ترموگرافی بسیار مفید است ترموگرافی کانال کابلهاست. با توجه به اینکه معمولا کانال کابلها کمتر مورد توجه قرار می گیرد و در صورت اتفاق باعث آسیب های گسترده و آتش سوزی خواهد شد پیشنهاد می شود بصورت دوره ای ترموگرافی انجام شود. شکل ۹ یک نمونه ترموگرافی کانال کابلها نشان داده شده است.
پیشنهاد می شود ترموگرافی تجهیزات الکتریکی حداقل سالی یکبار انجام شود.
[۱] National electrical manufacturers association
پایش متغیرهای دود خروجی دودکش در واحدهای صنعتی و نیروگاه ها
در واحدهای صنعتی و نیروگاهها، دود خروجی به طور منظم پایش شده و متغیرهای دود خروجی شامل SOx، NOx، O۲، CO۲، CO و … در بازه های زمانی مشخصی اندازه گیری می شود و با توجه به نتایج اندازه گیری، وضعیت احتراق تحلیل می گردد. به عنوان مثال، در این خصوص به موارد ذیل می توان اشاره نمود.
الف) با اندازه گیری CO و CO2، احتراق ناقص در بویلرها مشخص می شود و این نتایج به تنظیمات دمپرهای دود و هوای مشعلها کمک شایانی می نماید.
ب) NOx و SOx و CO۲ از آلاینده های اصلی صنایع هستند و با سنجش دوره ای آنها، تلاشهای لازم جهت بهبود شرایط احتراق و کاهش آلاینده ها شامل تنظیم مجدد ترکیب سوخت و هوای مشعلها و احتراق با هوای بهینه (به منظور کاهش CO و NOx) انجام می شود.
ج) در صنایع، با سنجش اکسیژن خروجی از دودکش، وضعیت هوای اضافی ورودی به مشعلها بررسی می گردد و این نتایج به تنظیمات کنترل کننده های اکسیژن کمک می نماید.
د) در نیروگاه های بخار، با سنجش و پایش میزان اکسیژن خروجی از دودکش، میزان نشتی هوا در ایرهیترها مشخص می شود. این نتایج به تنظیمات مربوط به ایرهیترها و سیلهای آنها کمک می نماید که در نتیجه فلوی هوای احتراق و راندمان افزایش یافته و توان مصرفی اف دی فنهای بویلر کاهش می یابد.
دستگاه آنالایزر دود TESTO 350 از کاملترین انواع آنالایزرهای گازهای خروجی از دودکش می باشد که کارایی، دقت و پایداری زیادی دارد و می تواند گازهای مختلف خروجی از دودکش را اندازه گیری کند. این دستگاه در سیستم های احتراق نیروگاه ها، انواع بویلرها و مشعلها، پلنت های صنعتی و … استفاده می شود و به گونه طراحی شده که با انتخاب پروب مناسب بتوان میزان گازهای خروجی از دودکش را تا دمای ۱۸۰۰ درجه سانتیگراد اندازه گیری نمود. نمونه ای از دستگاه آنالیز دود در شکل ۱ آورده شده است و شامل بخش های مختلفی است که در ادامه، برخی از کاربردهای آنها ارائه شده است:
الف – Analysis box
- اندازه گیری گازهایO۲ , CO, NO, NO۲, SO۲، HC، H2S, CO۲ و دما و محاسبه هوای اضافه
- دارای واحد آماده سازی گاز جهت کندانس گاز خروجی و جذبH2O
- محاسبه نقطه شبنم
- دارای قابلیت Gas dilutionجهت بالا بردن رنج اندازه گیری گاز
- فیلتر مخصوص برای پراب ها جهت اندازه گیری در محیطهای با غبار بالا
ب- Control Unit
- قابلیت برنامه ریزی برای اندازه گیری دراز مدت
- دارای حافظه جهت ذخیره اطلاعات
- قابل اتصال به دستگاه آنالایزر
- دارای پرینتر در کنترل یونیت
- نمایش همزمان ۶ متغیر در صفحه نمایش
- قابل اتصال به کامپیوتر توسط پورت سریال
- پراب اندازه گیری دما، رطوبت، سرعت گاز، فشار، تلاطم
- پراب اندازه گیریمتغیرهای دود
- دارای تاچ اسکرین و قلم مربوطه
پ- سنسورها :
- سنسور الکترو شیمیایی (O۲ , CO, CO۲, NO, NO۲, SO۲, HC, H۲S)
در شکل ۲ ماژولهای دستگاه نشان داده شده است:
نمونه ای از اندازه گیری متغیرهای دود خروجی در یک واحد نیروگاهی بخار نیز در جدول ۱ آورده شده است:
اندازه گیری فلوی سیالات در صنایع و نیروگاه ها
امروزه اندازه گیری جریان سیال بعنوان یکی از مهمترین پارامترهای اندازه گیری در صنایع مختلف و نیروگاه ها از اهمیت ویژه ای برخوردار است. در حقیقت اغلب کارشناسان پس از اندازه گیری دما، مهم ترین کمیت اندازه گیری در صنایع را فلو یا جریان سیال میدانند. با توجه به اهمیت اندازه گیری این کمیت و همچنین تنوع فرآیند صنایع گوناگون، در طول زمان روشهای مختلفی برای اندازه گیری جریان سیال بوجود آمده است. انتخاب فلومتر مناسب برای هر کاربرد نیاز به دانش کلی نسبت به روشهای گوناگون فلومتری و در نظر داشتن پارامترهای اصلی اندازه گیری از قبیل دقت، قیمت تمام شده، هزینههای تعمیرات و کالیبراسیون، سازگاری عملکرد فلومتر با شرایط پروسه تولید و… میباشد. به عنوان نمونه از انواع فلومترهای متداول در صنعت می توان به فلومتر جرمی کوریولیس، فلومتر الکترو مغناطیسی، فلومتر جریان گردابی، فلومتر لوله ونتوری، فلومتر از نوع روتامتر و فلومتر اولتراسونیک اشاره کرد.
فلومتر اولتراسونیک
استفاده از فلومتر آلتراسونیک برای اندازه گیری فلو یکی از روش های پرکاربرد است. در فلومتر آلتراسونیک از فرستنده و گیرنده های موج فراصوت استفاده می شود که فرستنده موج فراصوت در یک طرف لوله و گیرنده آن در طرف دیگر یا با فاصله از فرستنده قرار میگیرد. مدت زمان عبور موج از لوله، بستگی به مشخصات لوله و جنس سیال عبوری دارد که در یک اندازه گیری خاص، ثابت است و در کالیبراسیون دستگاه منظور میگردند. همچنین این مدت زمان، بستگی به جهت و سرعت عبور سیال در لوله نیز دارد. بنابراین با اندازه گیری فاصله زمانی بین ارسال موج توسط فرستنده و دریافت آن به وسیله گیرنده، می توان سرعت سیال و در نتیجه میزان فلو را بدست آورد. استفاده از امواج اولتراسونیک، اندازهگیری دبی حجمی طیف وسیعی از گازها و مایعات را امکانپذیر میسازد. در این فلومترها مواردی مانند هدایت الکتریکی، فشار، دما و ویسکوزیته اهمیت ندارند. مزیت عمده این گونه اندازه گیرها این است که هیچ گونه اثری بر روی کمیت مورد اندازه گیری ندارند و به علاوه از دقت و سرعت خوبی برخوردار هستند. در شکل های زیر چند نمونه فلومتر آلتراسونیک مشاهده میشود. در نمونه سمت چپ سنسورها از بیرون لوله نصب شده و برای اندازهگیری دبی سیالات خورنده مناسب است. نمونه سمت راست در داخل لوله قرار میگیرد. شکل پایین فلومتر مورد استفاده در نیروگاه را نمایش میدهد.
در این نوع از تجهیزات، از دو سنسور استفاده میشود که در کنار یکدیگر نصب شدهاند. هر دو سنسور میتوانند به صورت متناوب به عنوان فرستنده و گیرنده عمل کنند. مدت زمانی که طول میکشد موج اولتراسونیک از فرستنده به گیرنده برسد، معیاری از دبی سیال داخل لوله است. به همین دلیل، این فلومتر محدود به قطر منحصر به فردی از لوله نیست و میتوان از آن در اندازههای مختلف استفاده کرد. همچنین هیچگونه قطعه متحرکی در ساختار تجهیز استفاده نشده است. همین موضوع موجب میشود نیاز به تعمیرات به حداقل برسد.
معرفی فلومتر FLUXUS ADM 6725
فلومتر مذکور ساخت شرکت FLEXIM آلمان بوده و برای اندازه گیری فلو در لوله ها به روش آلتراسونیک مورد استفاده قرار می گیرد و بر اساس روش زمان انتقال (transit time) کار می کند. شکل زیر فلومتر مورد استفاده در نیروگاه را نمایش میدهد:
برخی مشخصات و ویژگی های فلومتر مورد استفاده عبارتند از:
- پنل جلو (Front Panel): پنل جلویی برای نمایش مقادیر فلو، ورود اطلاعات از طریق صفحه کلید دستگاه و اتصال کابلهای ترانسدیوسر میباشد.
پنل عقب (Rear panel): برای اتصال کابل تغذیه، محل اتصال کابل رابط سریال به کامپیوتر یا پرینتر و همچنین ورودی و خروجی های فرآیند (در صورت انتخاب) در نظر گرفته شده است.
- ترانسدیوسر و کابلهای اتصال (شکل پایین): روی ترانسدیوسر جهت فرضی حرکت سیال حکاکی شده است. اگر جهت جریان واقعی سیال هم جهت فلشها باشد، مقدار فلو با عدد مثبت نمایش داده میشود.
سنسورهای این دستگاه برای دمای سیال -۳۰ تا ۱۳۰ درجه سانتیگراد مورد استفاده قرار می گیرند که در بازه زمانی کوتاه، افزایش دما تا ۳۰۰ درجه سانتیگراد نیز قابل امکان پذیر است.
- اندازه گیری در لوله هایی از جنسهای معمول مانند استیل، مواد مصنوعی، شیشه، مس و با قطر لوله (Output Diameter) 10mm تا ۶۵۰۰mm قابل انجام میباشد.
- این فلومتر در هر جایی که دیواره لوله و مایع از نظر صوتی هادی باشند می تواند استفاده گردد. همچنین برای لوله های حاوی مواد همگن و برای مایعاتی که ذرات جامد خیلی ریز و حبابهای گاز حمل می کنند نیز مناسب است.
- در لوله های دارای lining داخلی نیز امکان اندازه گیری فلو وجود دارد. برای این منظور باید در تنظیمات دستگاه در زمان اندازه گیری فلو نوع lining را مشخص نمود تا سرعت صوت در آن در نظر گرفته شود.
- علاوه بر اندازه گیری فلو، در صورت سفارش پراب و تجهیزات مخصوص می توان سرعت صوت در سیال، ضخامت دیواره لوله و غلظت مواد تشکیل دهنده یک سیال محلول را اندازه گیری نمود.
- فلومتر FLUXUS از نوع قابل حمل بوده و علاوه بر کار با برق ۲۲۰V AC قابلیت کار با باتری ۱۲V DC نیز داشته و از این نظر برای استفاده در موقعیت های مختلف در صنعت مناسب است.
ارتباط با ما
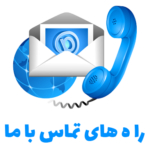
خدمات ترموگرافی توسط دوربین پیشرفته و تحلیل کارشناسان مجرب برای کلیه تجهیزات در تمامی شرکتهای استان خراسان قابل انجام است.
جهت اطلاعات بیشتر با
شماره مستقیم
۰۵۱۳۵۴۲۱۹۲۰
یا ایمیل
info@tpgm.ir
تماس حاصل فرمایید.